Small four-wheel tractor common fault diagnosis
Author:Ricdro
Among the more than 10 million tractors in China, small four-wheel tractors account for 60%, which is the main agricultural power machinery. In order to improve the efficiency of the use of small four-wheel tractors, the operator must not only have skilled driving skills, but also master troubleshooting and maintenance methods.
(1) The brake drum is hot. A Dongfanghong-180 small four-wheel tractor has not worked for a long time. It is found that the brakes are hot and hot, and the empty car is also overloaded when it is uphill. After inspection, the reason is that the driver adjusts the brake too tightly for driving safety, and the brake pedal free travel is almost zero. In this way, not only the engine power is consumed during running, but also the wear of the brake band is accelerated, causing the brake drum to generate heat. After the brake lever is adjusted, the pedal free travel is adjusted to 30mm, the brake is reliable, and the brake drum is no longer heated.
(2) The steering wheel is idling. A small red-wheel tractor of the Dongfanghong-170, which has been used for many years, found that the steering wheel and the steering wheel could not operate synchronously during the internship. After the right turn is made, when the left turn or the positive direction is reversed, the steering wheel is idling, the guide wheel is not deflected, and the right turn is flexible and the left turn is sluggish. Upon inspection, it was found that the turbine shaft and the steering vertical arm were not splined, but were fixed by a flat key (now the new factory tractors are all splined). Due to the long use time, the keys and the keyway are severely worn. When the steering wheel rotates under the control of the steering wheel, the steering vertical arm does not swing with it, so that the steering force cannot be reliably transmitted between the steering wheel and the guide wheel, causing the steering wheel to idle. . The keyway is properly trimmed and enlarged, and the corresponding flat key is added to assemble the test drive, and the steering returns to normal.
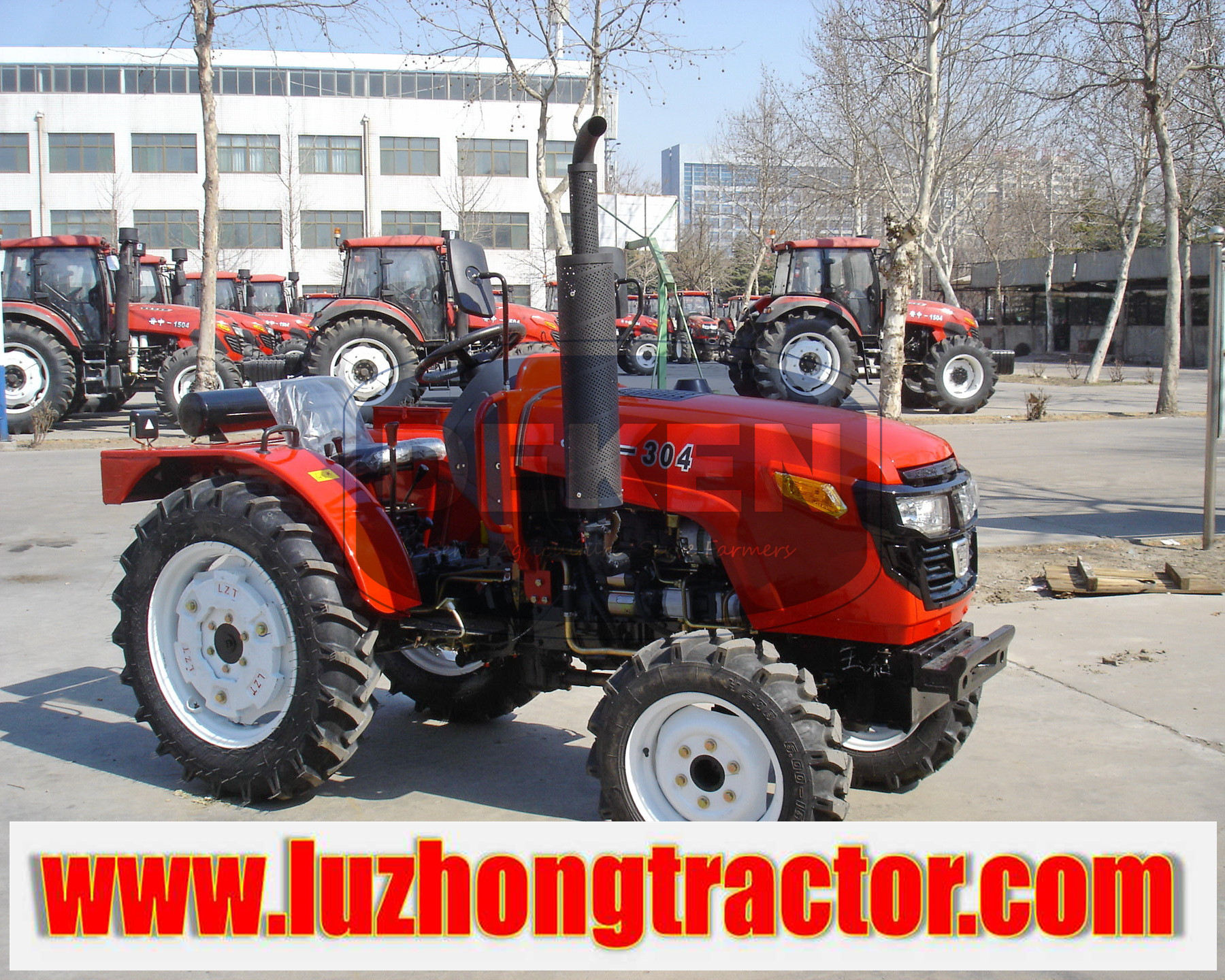
(3) The front wheel toe is normal, but the guide wheel accelerates wear. Several small four-wheel tractors have been used for less than one year, and the wear of the guide wheels has reached the end of the scrapping limit. After inspection, the front wheel toe value is in the range of 6 to 12 mm, which is a normal value. Further analysis and inspection found the reason for the excessive wear of the guide wheel: First, the inner and outer bearings of the guide wheel axle need to check the adjustment gap and add butter after 200 to 300 hours, but most of the robots do not do so, resulting in excessive bearing clearance. The front wheel is shaking. Second, the bracket bushing of the steering knuckle shaft is severely worn, the positioning force is lowered, and the front wheel is shaken, which is an important reason for the early wear of the front wheel. Solution: Replace the new bushing, or insert a copper washer into the bushing according to the gap after wear, and regularly fill the bushing. After the above maintenance, the guide wheel wears normally and the life is extended to 2 to 3 years.
(4) The clutch release bearing is hot or damaged. A belt-rotating small four-wheel tractor clutch release bearing is a sealed one-way thrust ball bearing. The design requires only a small axial thrust (the bearing force is about 260-320kg when separated), and generally does not bear radial force. In the work, the separation bearing rotates along with the clutch shell, and the hand-contacting and separating the bearing after parking has a hot feeling. The reason is that the clutch has no separation gap (due to improper adjustment or the clutch is not adjusted in time after the clutch is worn), so that the separation bearing rotates with the separation lever. This not only affects the normal operation of the clutch, but also causes the separation bearing to heat up and the operation time is long and damage is caused. It should be adjusted as required to maintain a normal clearance between the separation lever and the release bearing.
(5) Causes and elimination of the swinging shaft. A Dongfanghong-200 small four-wheel tractor suddenly slammed the front axle swinging shaft during transportation, and fortunately the handler handled it in time to avoid a vicious accident. The reason is that the newly-changed swing shaft positioning lock piece is too thin, the deformation is damaged during work, and the positioning function is lost. When inspecting similar faults, we also found that some of the operators used wire winding instead of the positioning locks, and thus the above-mentioned failures caused the car to be destroyed. Therefore, it is necessary to replace the new locking piece and never use a thin locking piece or a wire.
(6) There is a fierce “gritting” sound when traveling at high speed and low speed. This sound appears in the gearbox body, which is the signal that the differential case and the cover are about to “cut the neck”. If the violent “bite” sound becomes a percussion sound, it means that the “cut neck” has occurred, and the differential and Parts in the gearbox have been severely damaged. When you suddenly hear the “squeaky” sound in the driving, you should stop immediately to prevent the “cut neck” failure and avoid loss. Maintenance of the differential should be carried out in the usual steps.